About Us
HISTORY
Polycrete® was founded in Montreal, Quebec in 1988 by Serge Meilleur and André Grenon with the introduction of the first Polycrete® Insulated Concrete Form product: FLEX 850.
The newly patented product rapidly became an industry favorite due to its easy installation, its versatility and its superior strength. The FLEX 850 proved itself a product of excellence in more than fifteen countries through projects of all sizes and types. The FLEX 850 was recognized by the industry multiple times and received its first Domus Award for its energy saving excellence during Canada’s January 1990 Expo Habitat.
In 1997, Polycrete® FLEX 850 was selected as the product of choice for the construction of a new student housing project for the University of Quebec (ETS). This seven-story dormitory building was to be one of the world’s first ICF structures of more than three stories. The result was that the project was completed six weeks ahead of schedule within budget.
At the end of the 90s, Polycrete® decided to innovate again by developing a new generation of more high performance and economical products. These products, known as the P2, were thinner (1½” thick instead of the usual 2½”) nearly unbreakable, and consisted of composite panels reinforced by an embedded steel wire mesh. That is how in 2000, Serge Meilleur and André Grenon dedicated themselves into the design and building of the P2 manufacturing equipment.
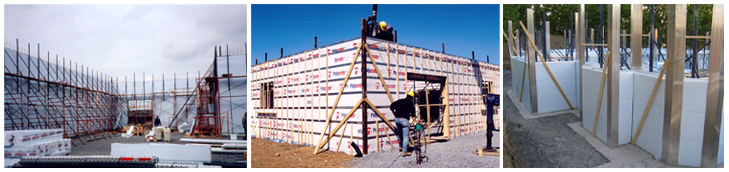
The solution was so attractive and efficient that a Japanese customer of the FLEX 850 decided to buy the new technology before its release on the market. In August 2001, the P2 manufacturing plant was successfully installed in Japan.
Always dedicated to improving their products and methods, in 2005 Polycrete® began to develop a new insulating formwork system for concrete: the Big Block. The Big Block merges the strengths of both the FLEX 850 and the P2. Joining the expanded polystyrene of the FLEX 850 to the embedded steel wire mesh of the P2, the Big Block embodies an extreme sturdiness and is able to withstand high lateral pressure during the concrete pour (1,600 lbs/sf or 75kPa).
All Big Block panels are fully assembled during the manufacturing process. Since the forms fold flat, they take less space for storage and transportation. At sixteen square feet (1.49 m2), the Big Block is the largest ICF available. In order to maintain our superior quality, the Big Block manufacturing process is closely controlled by Polycrete®. All Big Block products are manufactured on Polycrete® equipment and no contract manufacturers are employed.
VISION
By 2020, a significant portion of the residential and commercial building market will be built from insulating formworks for concrete, replacing the conventional structures that will be costly and inefficient on an ecological and performance point of view.
OUR MISSION
To conceive and promote methods and solutions to facilitate the construction of all types of buildings by using insulating formworks for concrete and in respect of the environment while keeping a high level of quality of products, training and services. |